Como Realizar um Eficaz Teste de Válvulas para Garantir a Segurança do Equipamento
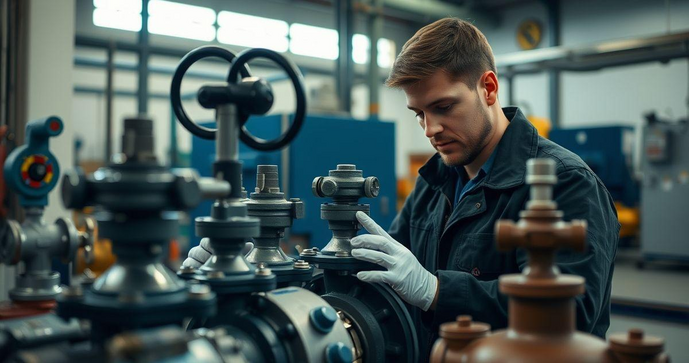
Por: Rosangela - 24 de Abril de 2025
Importância do Teste de Válvulas na Indústria
A importância do teste de válvulas na indústria não pode ser subestimada, pois essas componentes desempenham um papel vital na operação segura e eficiente de sistemas mecânicos e de controle de fluidos. Válvulas são responsáveis por regular o fluxo de líquidos e gases, garantir pressões adequadas e proteger equipamentos contra danos. Assim, garantir que funcionem corretamente é essencial para evitar falhas catastróficas.
Um teste eficaz das válvulas pode prevenir acidentes e garantir a conformidade com normas de segurança. Por exemplo, válvulas que não vedam adequadamente podem resultar em vazamentos, o que pode provocar incêndios, explosões ou contaminação ambiental. Além disso, a manutenção preventiva identifica problemas antes que se tornem críticos, prolongando a vida útil das válvulas e reduzindo custos operacionais.
Realizar testes periódicos também facilita a detecção de falhas sutis que, se não abordadas, podem levar a interrupções na operação. Em setores como o petroquímico, o farmacêutico e o alimentício, onde a precisão e a segurança são cruciais, a confiança em válvulas testadas adequadamente garante a continuidade do processo produtivo sem riscos.
Portanto, a realização de testes de válvulas deve ser vista como um investimento em segurança e eficiência, tornando-se um procedimento padrão nas operações industriais.
Tipos de Válvulas e suas Funcionalidades
Existem diversos tipos de válvulas, cada uma projetada para desempenhar funções específicas dentro de sistemas de controle de fluidos. A compreensão das características e funcionalidades de cada tipo é fundamental para garantir a escolha correta para cada aplicação. A seguir, apresentamos alguns dos principais tipos de válvulas comuns na indústria e suas respectivas funções:
1. Válvula de Globo: Projetada para regular o fluxo de fluidos, a válvula de globo é ideal para aplicações que exigem controle fino do fluxo. Ela possui uma estrutura que permite ajustes precisos, sendo muito utilizada em sistemas que operam em altas pressões.
2. Válvula de Esfera: Conhecida pela sua capacidade de abrir e fechar rapidamente, a válvula de esfera proporciona um baixo atrito e um fluxo contínuo. É amplamente utilizada em aplicações de barramentos, onde a minimização de restrições ao fluxo é crucial.
3. Válvula de Borboleta: Essa válvula é leve e ocupa pouco espaço, funcionando como um regulador de fluxo. A sua estrutura permite operação rápida, sendo bastante utilizada em sistemas de água e esgoto, além de aplicações em indústrias de alimentos e bebidas.
4. Válvula de Refluxo: Essa válvula é desenhada para permitir que o fluxo siga apenas em uma direção, evitando o retorno do fluido. Isso é crucial em sistemas onde a contaminação cruzada deve ser evitada, como em bombas e tubulações de saneamento.
5. Válvula de Retenção: Também conhecida como válvula de não retorno, a válvula de retenção é projetada para impedir o fluxo reverso, protegendo máquinas e equipamentos de danos. Elas são frequentemente empregadas em sistemas de abastecimento de água e aplicações de HVAC.
6. Válvula de Controle: Utilizada para regular a pressão e o fluxo dentro de um sistema, a válvula de controle ajusta a quantidade de fluido que passa através dela com base nos sinais de um controlador automático. Ela é essencial em processos que requerem variação precisa de fluxo.
A escolha do tipo de válvula adequado é essencial para garantir a eficiência e a segurança dos sistemas. Cada válvula possui características específicas que devem ser alinhadas às demandas operacionais para obter um desempenho ideal.
Métodos Comuns para Realizar o Teste de Válvulas
Realizar o teste de válvulas é um procedimento fundamental para garantir sua funcionalidade e segurança. Existem diversos métodos comumente utilizados para efetuar esses testes, cada um com suas características e aplicações específicas. A seguir, apresentamos algumas das principais abordagens para testar válvulas:
1. Teste de Pressão: Um dos métodos mais utilizados, o teste de pressão envolve a aplicação de uma pressão interna à válvula, superando a pressão operacional. Isso permite verificar se há vazamentos ou falhas na vedação. Os testes de pressão podem ser realizados com água ou ar, dependendo da aplicação e das normas exigidas.
2. Teste de Cercamento: Esse método avalia a capacidade da válvula de manter a vedação sob pressão. No teste de cercamento, a válvula é submetida à pressão de operação e, em seguida, observam-se os níveis de vazamento e a eficácia da vedação. Este teste é crucial para garantir a segurança dos sistemas que utilizam fluidos perigosos.
3. Teste de Funcionamento: Consiste em abrir e fechar a válvula diversas vezes para avaliar seu desempenho e resposta. Este teste permite identificar problemas de movimentação, desgaste ou irregularidades na operação. É comum que esse método seja feito em conjunto com outros testes de pressão.
4. Teste de Vácuo: Esse método é utilizado para válvulas que operam em sistemas de vácuo. Um teste de vácuo ajuda a verificar a integridade da vedação quando a válvula é submetida a condições de pressão reduzida. Isso garante que a válvula mantenha a operação eficiente em processos que dependem de vácuo.
5. Inspeção Visual: Embora não seja um teste formal de funcionamento, a inspeção visual regular é essencial para detectar sinais de desgaste ou danos nas válvulas. Isso pode incluir verificações de corrosão, folgas nas partes móveis e acumulação de sujeira que podem afetar o desempenho.
6. Testes Não Destrutivos (NDT): Métodos como ultrassons, raios X e testes de partículas magnéticas podem ser utilizados para inspecionar a integridade dos materiais da válvula sem danificá-la. Esses testes ajudam a detectar falhas internas que poderiam comprometer a segurança e eficácia da válvula a longo prazo.
A escolha do método adequado para o teste de válvulas deve levar em consideração fatores como o tipo de válvula, a aplicação e os requisitos de segurança específicos de cada sistema. A realização periódica desses testes é fundamental para garantir a operação segura e eficiente de toda a instalação.
Equipamentos Necessários para o Teste de Válvulas
A realização de testes de válvulas requer o uso de equipamentos apropriados para garantir a precisão e a segurança do procedimento. A seleção correta dos instrumentos é crucial para obter resultados confiáveis.
A seguir, listamos os principais equipamentos necessários para realizar o teste de válvulas:
1. Manômetro: O manômetro é um dispositivo fundamental para medir a pressão dentro da válvula durante os testes. Ele permite monitorar a pressão aplicada e verificar se a válvula suporta os níveis exigidos sem apresentar vazamentos.
2. Bomba de Teste: Utilizada para aumentar a pressão interna da válvula, a bomba de teste é essencial, especialmente em procedimentos de teste de pressão. Existem bombas manuais e elétricas, sendo a escolha dependente do tipo e da aplicação da válvula.
3. Equipamento de Vácuo: Para testes de válvulas que operam sob condições de vácuo, um equipamento de vácuo é necessário. Esse aparelho é responsável por gerar a condição de teste adequada, permitindo verificar a vedação da válvula sob pressão negativa.
4. Conectores e Mangueiras: Conectores e mangueiras adequados são essenciais para a ligação entre a válvula e os outros equipamentos de teste. A seleção de materiais resistentes e compatíveis com os fluidos a serem testados é crucial para evitar vazamentos.
5. Ferramentas de Montagem: Ferramentas como chaves de fenda, chaves inglesas e alicates são necessárias para a instalação e a desmontagem das válvulas antes e após os testes. Estas ferramentas também são úteis para ajustar componentes e verificar a posição da válvula.
6. Equipamentos de Segurança: Desde óculos de proteção até luvas e protetores auditivos, os equipamentos de segurança são indispensáveis durante o procedimento de teste. Garantir a segurança dos operadores é uma prioridade, especialmente quando se trabalha com pressões elevadas e fluidos potencialmente perigosos.
7. Dispositivos de Registro: Para documentar os resultados dos testes, dispositivos de registro ou planilhas digitais são úteis. Esses registros ajudam a manter um histórico da performance da válvula e são essenciais para auditorias e cumprimento de regulamentações.
O uso adequado desses equipamentos assegura um teste eficaz das válvulas, contribuindo para a segurança e a funcionalidade dos sistemas industriais. Portanto, a preparação antes de iniciar os testes é fundamental para o sucesso do procedimento.
Interpretação dos Resultados dos Testes de Válvulas
A interpretação dos resultados dos testes de válvulas é uma etapa crítica que exige atenção aos detalhes e conhecimentos técnicos.
Os resultados obtidos durante os testes fornecem informações valiosas sobre o desempenho e a integridade das válvulas.
A seguir, discutimos como interpretar esses resultados de forma eficaz:
1. Verificação da Vedação: Um dos principais objetivos dos testes de válvulas é avaliar a vedação.
Se o teste de pressão mostrar vazamentos, é crucial identificar a origem do problema.
Os vazamentos podem indicar falhas na junta, desgaste, ou danos na superfície de vedação da válvula.
2. Leitura do Manômetro: Durante os testes, as leituras do manômetro são fundamentais.
Se a pressão se estabilizar conforme esperado, isso indica que a válvula opera dentro dos limites normais.
Por outro lado, uma pressão que cai rapidamente pode indicar um vazamento ou falha na vedação.
3. Análise de Ruídos: No teste de funcionamento, qualquer ruído anormal, como rangidos ou estalos, deve ser investigado.
Esses sons podem sugerir problemas mecânicos, como peças soltas ou desgastadas, que podem comprometer a operação da válvula.
4. Desempenho sob Condições de Vácuo: Para válvulas operando em condições de vácuo, observar a manutenção da pressão negativa é essencial.
Uma perda de vácuo pode indicar falhas que devem ser corrigidas antes do reuso da válvula.
5. Comparação com Padrões de Referência: Os resultados dos testes devem ser comparados com os padrões e especificações fornecidos pelo fabricante.
Esses padrões oferecem uma referência sobre o que é considerado um desempenho aceitável e ajudam a identificar desvios que indicam necessidade de manutenção.
6. Documentação dos Resultados: É importante registrar todos os resultados de forma detalhada, incluindo dados de pressão, observações e condições do teste.
Essa documentação é vital não apenas para auditorias, mas também para futuras manutenções e reavaliações do desempenho da válvula.
A interpretação correta dos resultados dos testes de válvulas não apenas assegura a operatividade do sistema, mas também contribui para a segurança e eficiência das operações industriais.
Portanto, é essencial que a equipe responsável pela execução e análise dos testes tenha o conhecimento adequado e prática para realizar uma avaliação precisa.
Manutenção Preventiva e Recomendação pós-teste
A manutenção preventiva é uma prática crucial para garantir o funcionamento seguro e eficiente das válvulas e, após a realização dos testes, é vital seguir recomendações específicas para assegurar que as válvulas permaneçam em boas condições.
A seguir, apresentamos orientações sobre manutenção preventiva e recomendações pós-teste:
1. Programação de Manutenção Regular: Estabelecer um cronograma de manutenção preventiva é fundamental para identificar e corrigir problemas antes que se tornem críticos. A frequência dessa manutenção pode variar dependendo da aplicação, mas recomenda-se realizar inspeções pelo menos uma vez por ano.
2. Limpeza das Válvulas: Realizar a limpeza das válvulas regularmente ajuda a remover sujeira, detritos e corrosão que podem afetar a operação. Utilize produtos de limpeza compatíveis com os materiais da válvula e evite soluções abrasivas.
3. Lubrificação das Partes Móveis: A lubrificação adequada dos componentes móveis é essencial para prevenir o desgaste e garantir uma operação suave. Aplique lubrificantes recomendados pelo fabricante, seguindo as diretrizes para frequência e tipo.
4. Monitoramento de Vazamentos: Após os testes, faça um acompanhamento contínuo em busca de sinais de vazamentos. Inspecione as juntas e superfícies de vedação, pois são áreas críticas que podem apresentar falhas ao longo do tempo.
5. Revisão da Configuração da Válvula: Após ajustes realizados nos testes, verifique se a configuração da válvula está de acordo com as normas e requisitos operacionais. Isso inclui a verificação das posições das válvulas, pressão de operação e funcionalidade adequada.
6. Treinamento da Equipe: Forneça treinamento regular para a equipe responsável pela operação e manutenção das válvulas. A educação contínua sobre novas tecnologias, procedimentos de teste e manutenção pode ajudar a prevenir erros e promover a segurança.
7. Registro de Dados: É essencial manter registros detalhados dos testes, manutenções e quaisquer correções realizadas. Essa documentação ajuda na análise de desempenho ao longo do tempo e permite identificar padrões que possam indicar a necessidade de intervenções mais abrangentes.
Seguir essas recomendações de manutenção preventiva e medidas pós-teste não apenas aumenta a durabilidade das válvulas, mas também assegura a segurança e a eficiência operacional em processos industriais. O investimento em manutenção preventiva é sempre mais econômico em comparação com a correção de falhas críticas.
A realização de testes de válvulas e a adoção de práticas de manutenção preventiva são essenciais para garantir a segurança e eficiência dos sistemas industriais. Ao compreender os diferentes tipos de válvulas, os métodos de teste e a importância da interpretação dos resultados, as indústrias podem minimizar riscos de falhas operacionais.
A manutenção regular e o seguimento de recomendações específicas contribuem para prolongar a vida útil dos equipamentos e otimizar a operação. Em resumo, investir tempo e recursos na manutenção e testes das válvulas é uma estratégia eficaz para assegurar um funcionamento adequado e seguro, promovendo a confiabilidade dos processos produtivos.